A comparison between the cities of Amsterdam (the Netherlands) and Barcelona (Spain), two fast growing cities which have both approached the smart city concept in different ways, leading to contrasting results in the degree of smart city projects and their ability to upscale those projects.
Want to receive updates like this in your inbox?
Get notified about new updates, opportunities or events that match your interests.
Maybe you will also like these updates
Recap of Knowledge- and Demoday #26: Learnings from our network
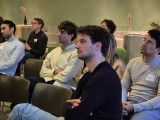
Last Thursday, December 12, we gathered at film house Lab111 for the last Knowledge- and Demoday of the year. Together with the network, we celebrated the festive close of 2024, reflected on the lessons learned over the past year, and took a look ahead at the future. The day featured and engaging Knowledge Sessions by DRIFT and dynamic 7-minute pitches where we shared insights from various innovation projects from the past year.
In this article, we’ll provide you with a quick overview of the Knowledge Session and Pitches.
About our Demodays
The Demodays are one of the tools we use to stimulate innovation and encourage connection between our partners and community. The purpose of the Demodays is to present the progress of various innovation projects, ask for help, share dilemmas and involve more partners to take these projects to the next level. More information about the Demodays can be found here.
Knowledge Session: The Business of Transition
Together with DRIFT (Dutch Research Institute for Transitions) we dove into the topic: the "Business of Transition." How can businesses embrace the concept of "radical change"? And how do they balance collective interests with self-interest? Teun Strikkers and Floor van den Elzen guided the audience through the complex world of systemic change and the role businesses play in these processes. Read Jills full report here.
Pitches
AMS Institute & University of Applied Sciences Amsterdam | ATELIER
Project Manager Omar Shafqat (University of Applied Sciences Amsterdam) and Urban Living Lab Developer Juanita Devis (AMS Institute) shared their experiences with the ATELIER project, an EU-funded Smart City initiative aimed at creating and replicating Positive Energy Districts (PEDs) within two Lighthouse Cities (Amsterdam and Bilbao) and six Fellow Cities.
Over the past year, they have worked on a tangible project: the actual development and implementation of an energy community and a positive energy district in the Buiksloterham neighbourhood in Amsterdam Noord. The buildings have been constructed, and residents have moved in. The programme will continue for another six months, during which the team will evaluate their impact, reflect on lessons learned, and explore how this model can be replicated in other cities across the globe.
The challenges they shared were diverse. For instance, there were issues related to governance and the community aspect: residents moved into the homes and subsequently became part of an energy community, without having actively chosen to do so. Such housing associations (VVE’s) require significant commitment and expertise. Meanwhile, the municipality also struggled to determine its role and relationship with this new community. Financially, there were hurdles as well. While this project benefitted from significant research funding and attention, it remains far more difficult to free up resources within regular development and construction processes to accelerate the implementation of PEDs. As a result, scaling up remains highly challenging and complex.
Finally, they discussed the need to maintain momentum and the importance of gathering and sharing their impact and lessons. This, too, requires considerable energy and is just as crucial as the success of the project itself. The Fellow Cities in the project are already adopting many elements, but to further disseminate this story, many more presentations and ongoing co-creation moments with various stakeholders in the field will be necessary.
While this project is well known within the network, it once again became clear that many in the audience were hearing about it for the first time. It seemed perfectly logical to them that this concept should be presented more often at the very start of planning and developing new neighbourhoods.
As a network, we also feel a responsibility to help spread this story, and we are delighted to announce that we will be collaborating on the Innovation Ateliers in the coming year. More on this to follow!
Municipality of Amsterdam | Circular Economy Monitor
By 2030, Amsterdam aims to reduce the use of new, non-renewable materials by 50%. An ambitious goal, but how do you actually measure that? Jorren Bosga from the City of Amsterdam shared more about this challenge.
The measurement process started five years ago, at a time when the circular economy was still in its infancy at the policy level. They gradually discovered which data was needed as they went along. By now, current and historical material flows have been mapped out, and connections to behaviour have already been established. Some surprising insights from this process include the fact that the average Amsterdam resident has a lower CO₂ footprint than the average Dutch citizen, and that the higher someone’s income, the higher their footprint tends to be.
The focus is now shifting towards the future, with a more detailed look at specific domains. Because the current situation has been mapped out, it becomes possible to ask questions like: What can we influence through policy? And how much material use or CO₂ reduction can we expect as a result?
Jorren also highlighted several challenges, particularly around data collection. These include linking data across different scales and from multiple sources. Measuring data across the full scope of the transition can encompass a vast number of sectors – think of construction, food, and consumer systems, among others. This sheer volume of data can be overwhelming, and maintaining it structurally adds another layer of complexity. Furthermore, the scale at which data is measured does not always align with the scale at which the municipality has influence.
Finally, Jorren emphasised to the network that insights are only useful if they lead to action. For his team, it is therefore essential to work closely with policymakers. He also pointed out that while it is important to measure impact to understand whether you are on the right track, ‘impact’ can mean many things. For instance: Should the datasets be as complete as possible, or is the growing interest in- and adoption of Circular Economy principles the ultimate goal?
Looking ahead to 2025, Jorren and his colleagues will, among other things, focus on making the Circular Economy Database more transparent and shareable, while also contributing to the new Circular Economy strategy for the City of Amsterdam. We’ll be keeping an eye on their progress!
Arcadis | The Healthy City Index 2024
Inge Noten and Renée Schoonbeek presented the Gezonde Stad Index (Healthy City Index). Every two years, Arcadis publishes this comparison of 25 cities. This is the third edition. Using public data, they compare how cities perform on the physical characteristics of a healthy city, as previously defined by the RIVM (National Institute for Public Health and the Environment).
This year, Apeldoorn was presented as the winner. Key factors contributing to this city’s higher score compared to others include its green character, an increase in active mobility without a corresponding rise in accidents, and a strong sense of safety and social cohesion (for example, through neighbourhood and community activities).
Some interesting general findings include that urban densification is happening everywhere, yet this can go hand in hand with greening efforts. Additionally, while active mobility is increasing, the number of accidents is also on the rise, likely due to increasingly busy cycle paths with varying speeds.
Inge and Renée emphasised to the audience how valuable it is to occasionally abstract data on a large, quantitative scale before diving deeper into the details. The overview provided by the index offers an excellent starting point for discussions with municipalities about what is currently working well or poorly. Moreover, while the index focuses on the physical environment, it only addresses one aspect of overall health. Therefore, collaboration and integration with other health-related themes are essential and very welcome.
Finally, a healthy city is never truly ‘finished’. Both the index and the cities themselves continue to evolve and improve.
Hieroo | Community Wealth Building and the “Buy Local”platform (Koop Lokaal Platform)
Mirna Nasr and Thomas Siderius gave an pitch about Community Wealth Building and the “Buy Local” platform in the Nieuw-West district of Amsterdam. They are collaborating within the framework of the National Program "Together New West," an initiative involving seven different parties in Nieuw-West. The goal is to strengthen the local economy through the Community Wealth Building (CWB) model, which aims to minimize extraction from the local economy. The idea is to circulate as much money as possible locally, for the benefit of the area's residents.
Community Wealth Building is an economic model focused on creating sustainable, local prosperity. This is done by strengthening local organizations and businesses so that the profits stay within the community. In Nieuw-West, the "Buy Local" platform is being developed as an initial phase of a potentially larger system, where local entrepreneurs, businesses, and residents directly benefit from the circulation of local money. The aim is to further develop this platform to strengthen the local economy and contribute to more than just the profits of entrepreneurs.
The "Buy Local" platform has been under development for some time, and at present, active discussions are being held with local entrepreneurs and residents to map out the needs and wishes of the community. One of the biggest challenges mentioned by Mirna and Thomas is the active mobilization and involvement of local network builders and entrepreneurs. While there is a lot of enthusiasm about the possibilities of the platform, it remains difficult to effectively activate existing networks. Another important aspect of platform development is learning by doing. This applies not only to the initiators but also to the involved entrepreneurs. Success stories play a crucial role here, as they show how local businesses can benefit from the platform and the local money system.
In 2025, Mirna and Thomas will focus on further developing the "Buy Local" platform and expanding the possibilities for local payments. Linking different types of accounts to the platform could be a way to integrate local subsidy forms, such as neighborhood budgets, into the system. They are also looking at examples from other cities, such as Santa Coloma in Spain, where shops use a local currency, and residents receive part of their benefits and allowances on a local account. This could be a great model for Nieuw-West.
Demoday #26: Knowledge Session on the Business of Transition
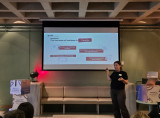
At the final Knowledge and Demo Day of the year, DRIFT (Dutch Research Institute for Transitions) presented an engaging session on the "Business of Transition." How can businesses embrace the concept of "radical change"? And how do they balance collective interests with self-interest? Teun Strikkers and Floor van den Elzen guided the audience through the complex world of systemic change and the role businesses play in these processes.
Teun began with a personal story from his time living in Norway, where he witnessed glaciers retreating. This experience prompted a critical question: why is it so hard to solve major problems like climate change?
He proposed several answers:
• Difficulty in defining boundaries (issues are interconnected).
• Problems occur across different times and locations.
• Attempts to solve problems sometimes exacerbate them.
• Disagreements not only about solutions but also about the nature of the problem itself.
• Problems are persistent or "sticky."
Teun explained that many challenges stem from the lack of clear boundaries within complex adaptive systems. These systems, like economies or energy networks, are made up of interconnected parts that constantly adapt to changes, making it hard to set boundaries or implement change.
What Are Transitions?
Transitions are fundamental, transformative changes that affect culture, structures, and practices. Teun referred to the traditional S-curve model often used to describe the lifecycle of transitions but introduced a more modern alternative: the X-curve. This model better captures the dynamics of transitions, highlighting the interplay between innovation and the dismantling of old structures.
The dynamics of a transition include:
Reconfiguration: What needs adjustment, redesign, or recalibration?
Consolidation: Which new principles and values should be formalized into norms, laws, and regulations?
Scaling: What initiatives require more support, investment, or visibility?
Phasing out: What needs to be retired, and how can this process be facilitated?
Entrepreneurship and Transitions
Floor focused on the practical side of transitions and the role of entrepreneurship. She noted that businesses often struggle to connect their daily operations with broader systemic changes. However, she emphasized, “The business of business is transitions” — companies must take responsibility for their role in driving sustainable change.
One illustrative example was the OV-fiets (a shared bicycle service), which started as a small initiative and grew into a nationwide success that promoted sustainable mobility. This example demonstrated how local innovations can contribute to systemic change, even without addressing all problems at once.
Floor also addressed the tension between short- and long-term goals, highlighting the challenge for businesses to balance collective interests with profitability. She spoke about the importance of creating a “learning environment” where businesses continuously reflect on their impact and adapt their strategies to a changing world. Innovation is all about experimentation: “learning by doing, and doing by learning.”
Tensions and Opportunities in Transitions
The session invited active participation from the audience, sparking interesting debates. One participant remarked, “Isn’t the business of business still just business?” Unilever's decision to sell the Vegetarian Butcher due to low profits showed how financial priorities can clash with sustainability goals.
Another discussion focused on the meaning of sustainability. For example, is Tesla still driving change, or is it mainly succeeding by meeting consumer demands? These questions encouraged thinking about what truly makes a company sustainable and how fairness can be part of transition strategies.
Learning from Inspirational Examples
In smaller groups, participants discussed companies like Patagonia, Dopper, and Interface that are succeeding in transitions. They explored why these companies thrive where others struggle and how other players can support such success.
The discussions emphasized the value of collaboration. Social learning — reflecting and experimenting together — was seen as key to driving big changes. One participant noted, “Our individual choices often conflict with what we choose as a group,” highlighting the need for collective action.
The session showed that while transitions are challenging, they are possible if we’re ready to think and act differently. Businesses play a vital role, not just in implementing changes but in leading the way with new models and practices.
Do you want to learn more about DRIFT and this topic? Leave a comment below and we’ll connect you with them!
🚀 Oproep voor organisaties in de publieke sector! Draag bij aan de ontwikkeling van ethische mobiele innovatie! 🌍
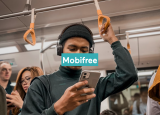
Wil jij de status quo uitdagen en bijdragen aan een mobiel ecosysteem dat privacy, duurzaamheid en ethische technologie vooropstelt?
💡 Bij Waag Futurelab zijn we vastbesloten om alternatieven te verkennen voor de datahongerige apps en apparaten die momenteel de techwereld domineren. Via ons onderzoeksproject Mobifree nodigen we organisaties in de publieke sector uit om een open-source Murena-smartphone te testen en samen met ons de toekomst van ethische, open-source mobiele technologie in Europa vorm te geven.
Dit is jouw kans om:
✅ Als organisatie Murena-smartphones te testen, voorzien van open-source apps.
✅ Feedback te geven die direct invloed heeft op de volgende generatie mobiele oplossingen.
✅ Bij te dragen aan een duurzaam, veilig en inclusief alternatief voor Big Tech.
🔍 Wat kun je verwachten?
- Doe mee aan een pilot van twee maanden (februari–oktober 2025) en verken hoe open-source tools jouw werk- en persoonlijke behoeften kunnen ondersteunen.
- Test baanbrekende technologie terwijl je pleit voor ethische en duurzame softwareontwikkeling.
- Maakt deel uit van een community die een privacy gerichte en Big Tech-vrije toekomst vormgeeft!
🙌 Wie kan deelnemen?
We een groep van maximaal 30 deelnemers om de volgende kerngebieden te verkennen:
- Besturingssystemen
- Messaging-apps
- Appstores
- Cloudservices
📩 Hoe kun je je aanmelden?
Stuur een e-mail naar bente[at]waag[dot]org met de naam van je organisatie, het aantal deelnemers, gekozen categorieën en een korte motivatie om mee te doen. Vervolgens zullen wij contact met je opnemen!
Doe met ons mee om mobiele technologie opnieuw vorm te geven voor een betere, privacy-respecterende Europa 🌟
@nancyzikken Thanks for the info! I've posted my thesis to the smart city academy :)
Hi Tijn, last week we opened a space on the Amsterdam Smart City platform where everyone can put online researches, investigations, tools and methodologies about the smart city. It is called the Smart City Academy. Would you like to add your research to this?
Please find the Academy here: https://amsterdamsmartcity.com/themes/smartcityacademy
You can add your contribution here: https://amsterdamsmartcity.com/academy/researches-and-theses. You can link to your research if you upload it on for instance Google Drive.
The link in this post doesn't seem to work anymore...